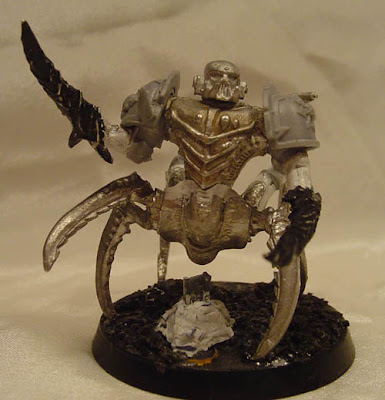
Hello everyone and welcome to another fun filled tutorial on Sculpting. For today's sample piece, we have the above Chaos Space Marine. Before anyone asks: NO THIS IS NOT A 'SARPEDON'. :-p I did this conversion before Soul Drinkers was even written. This guy was originally done up for the 3rd edition Chaos Codex to represent a Chaos Lieutenant with Daemonic Talons and Daemonic Speed. He was also my first experience with blue/white epoxy. It was such an "enjoyable" medium that I used the rest of it to fill gaps in terrain. I had to redo several pieces into Green Stuff too. Nowadays this miniature fields as a Chaos Lord with Daemon Weapon and then Steed of Slaanesh or Terminator Armour.
His abdomen and most legs are from an Epic Hunter-Screamer (also known as the RT era Carnifex), the torso is from a Phantom Titan, the arms from the metal Daemonettes, and the head and shoulder pads from Chaos Havocs.
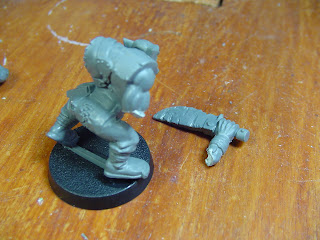
So how do we fix him up right proppa? With Green Stuff! Because even an Ork knows that glue is not gap filler.
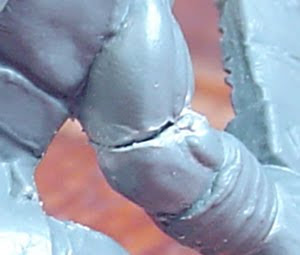
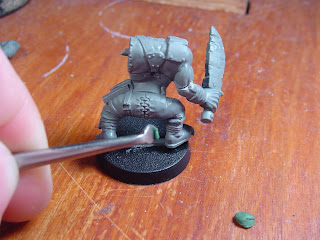
Scrape the putty off your knife so that it is generally where you want it. You will probably want to pause and wipe the blade off on a paper towel after this. A thin film or smear of putty will often adhere to the tip of your blade despite lubricant. This can build up and cause issues with smoothing and sticking. Take care of your tools and they'll take care of you.
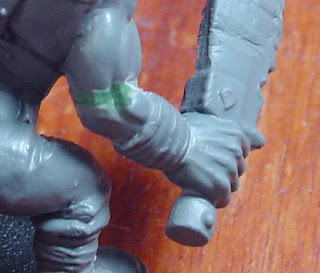
When shaping the putty, just pushing it into position is a good way to get it to stick to your sculpting tool. Instead, you want to use gentle sweeps of the smoother almost perpendicular to the crack to "draw" the putty down the line.
It is also easist to start in the center of the gap and shape the putty towards the ends. This will spread the putty more evenly and reduces the amount of cleanup needed along the edges.
When smoothing the putty, especially when thinning it at an edge or juncture, use a tight swirling motion to "polish" the putty down to shape.
The nicest thing about a small fill like this is that it is easy to follow the shapes of the original model. The plastic of the model will usually keep you from pressing in too deep and will guide your sculptwork.
As another note, I recommend starting out with organic models like Orks, Chaos or Tyranids... they are a little more forgiving towards small mistakes of shape, size, and smoothness.
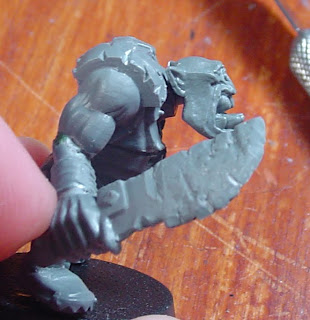
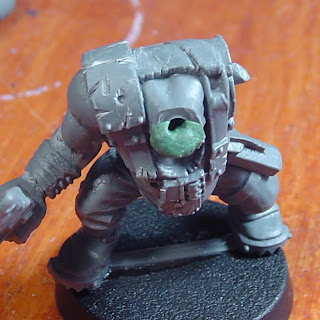
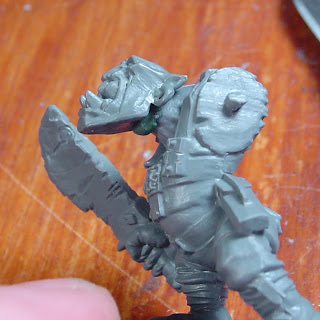
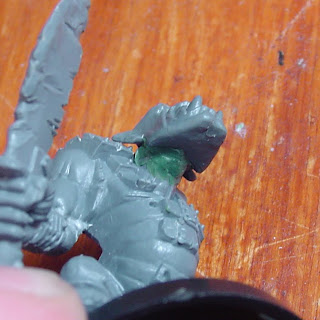
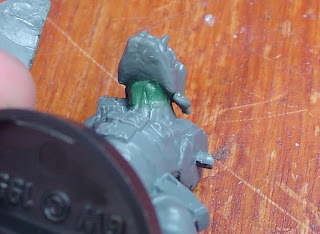
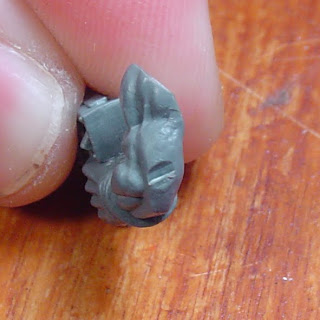
The trick with this repair is that it uses a very small amount of Green Stuff. Epoxy bonds to other epoxy very well, but not so much to plastic or metal in small amounts. There needs to be a decent amount surface area to adhere too, lest the finished product just flake off after curing.
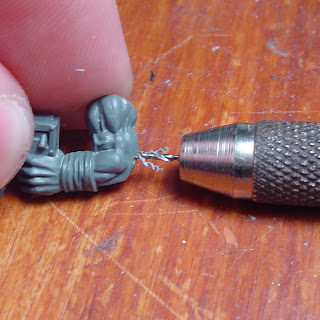
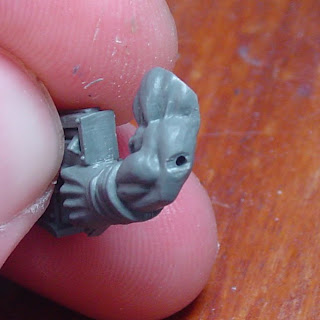
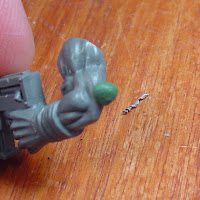
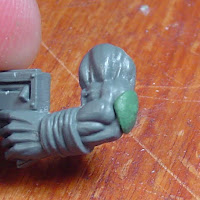
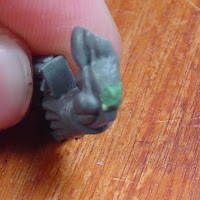
Now place a large ball of putty on the area. (Figure 1) Press it down slowly but firmly to fill into the hole. (Figure 2) Then use the blade edge of your tool to trim the excess away from the area. (Figure 3) Do this by pushing the edge into the putty to cut it and then scraping away from the center mass. You will want to make sure your blade is well lubricated so that you don't accidentally pull the putty off during this. The final result should be a rhombus in the general shape and quantity needed.
A raised fill is trickier than a recessed fill because you don't have the edges of the gap to keep you from pushing too far in. Put too much pressure on a raised feature and you'll just smoosh the whole thing flat. With the semi-solid nature of putty, trying to push a feature back up is often a frustration of creases, folds, slippage and bad words. It will often be easier to just wipe the putty off and apply a fresh ball. To avoid this, just use the same draw and burnishing techniques as above... with more care for depth.
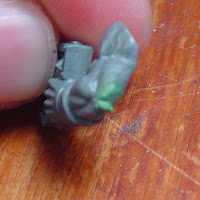
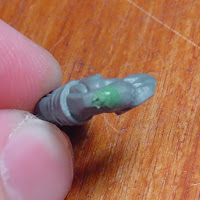
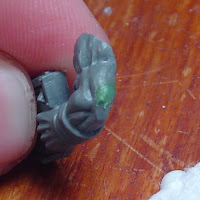
The big thing this changes is where you start your sculpt from. You can start from the depths and push everything up to higher areas... have fun with that. Or you can start from the highest points and draw the putty down to where you need. (Figure 1) Any excess putty gets worked down and away from the main sculpt. (Figure 2) Once you have it sufficiently thinned, you can scrape it off the model. (Figure 3) Any loose ends or scrape marks can then be burnished smooth.
Whew... made it all this way or did you just skim? :-p Hopefully this has been an interesting and informative tutorial. Next Week: "Sculpting 201: Pinning, Armature, and Large Shapes". Cheers!
Good stuff, to be sure.
ReplyDeleteThe motions are important, but something you might pick up with trial and error. At least, I did.
What I found most interesting was the tail end of it. I hadn't considered the use of drilling a small hole in there, but I can see how that would indeed make a difference.
Your preparation of the model was by far the most entertaining part of the article.
Keep up the good stuff, man.
Thanks for another great tutorial. They've been greatly appreciated.
ReplyDeleteAhhh the old CHaos Lord conversion, I got to giggle when I saw he hasnt gotten any paint yet- as I have several conversions just as old and just as paintless!
ReplyDeleteNice addition to the tutorial :)
@Raptor1313: I'm not certain I get you comment about the preparation of the model. The deliberate "mistakes" that I'm fixing up or the running commentary?
ReplyDelete@Rkik: Thanks!
@MoM: Actually, that's just the old pic. He's gotten painted, detail work and based. :-p I was just too lazy to take a new pic.
The stuff you did to break the model was comical. It might be me, but I'm always for adding a little bit of extra comedy here and there into writings when possible or appropriate.
ReplyDelete